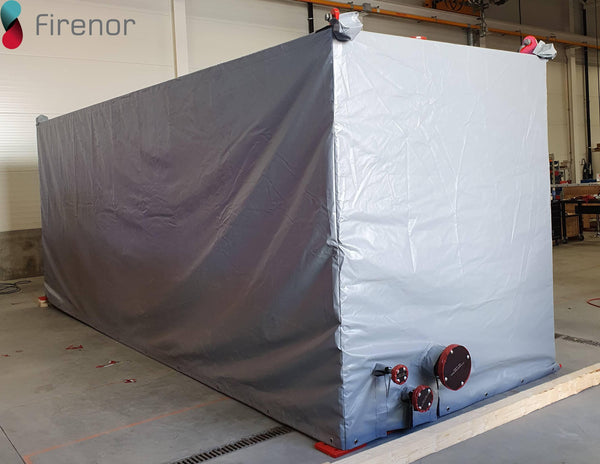
Case Study: Preserving Firenor's fire hydrants for shipping to Singapore
In March, we were contacted by Firenor regarding the preservation of a shipment of 48 fire hydrants and 1 deluge skid. Firenor has its head office in Kristiansand and supplies high-quality fire safety systems. They both design, manufacture and supply equipment all over the world, mainly for the oil and energy sector.
The hydrants had to be packed according to the customer's requirements/NORSOK - specially adapted flame-retardant tarpaulins with inspection doors, tag number, openings for flanges and lifting lugs and the flanges must be blinded.
« The equipment inside the wooden crate shall be covered with a flame retardant tarpaulin (minimum total weight 500gr/m2). The tarpaulin shall be tailor made for the package and provided with hatches/doors for enabling inspection and maintenance of preservation. If required, hatches/doors shall be included for access for lifting, electrical or instrument connections required during transportation, ie connections for electric heaters, motor space heaters, etc. Closing of hatches/doors shall be by means of zipper, Velcro (burr fasteners ), wire rope, etc. The equipment inside the wooden crate shall be covered with a flame retardant tarpaulin (minimum total weight 500gr/m2). The tarpaulin shall be tailor made for the package and provided with hatches/doors for enabling inspection and maintenance of preservation. If required, hatches/doors shall be included for access for lifting, electrical or instrument connections required during transportation, ie connections for electric heaters, motor space heaters, etc. Closing of hatches/doors shall be by means of zipper, Velcro (burr fasteners ), wire rope, etc ”
Based on the technical drawings, sketches of the tarpaulins were made, Firenor made requests and any changes before the drawings were approved and could be put into production. To be on the safe side, one of each size was ordered for trial fitting before the entire batch was put into production.
When the samples arrived, and they fit perfectly, the rest of the project was given the thumbs up. We produced 12mm waterproof veneer covers for the flanges while the factory sewed the remaining tarpaulins.
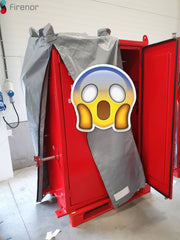
During the installation of the last tarpaulins, it turned out that the factory had sewn one too much of one size and one too little of the missing size
- the factory threw themselves around and sewed a new one and we sent it up with express shipping and delivered to the door the day before the deadline. The hydrants were then packed into crates before leaving
Kristiansand on the way to Singapore!
Good dialogue with the customer, effective problem solving and a good collaboration with our manufacturer made this a successful project and we look forward to more such assignments!